最速で短尺成形薪を成形する塩ビ管を作るのまき
コーキングガンでの圧縮ダンボール薪の成形では、押し出し時に内部で詰まりが起こり、反作用で塩ビ管が前方にズレてしまうため、ホルダーに塩ビ管をしっかりと固定する必要がありました。
最初はクランプやホースバンドで塩ビ管を固定していましたが、強い押し出し力に耐えられずズレてしまうことがあり、さらに着脱作業にも時間がかかって効率が悪いのが課題でした。
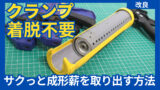
この問題に対処するため、クランプの代わりに同径の塩ビ管を縦に半割したストッパーを導入し、塩ビ管を手早く固定できるように改良しました。
しかしこの方法でも、毎回ストッパーやVUキャップを取り付け・取り外す手間が残り、連続作業には不向きでした。
さらに、成形前にダンボールのタネを詰める際、そのたびに塩ビ管をコーキングガン本体から取り外す必要があるという点も大きなストレスでした。
これらの課題を一気に解決するために、まず塩ビ管の先端にストッパー機能を一体化する加工を施し、別部品としてのストッパーすら不要にすることで、取り付け・取り外しの手間を完全に排除することにしました。
加えて、分岐継ぎ手を用いて横方向からタネを投入できる構造に変更し、塩ビ管を本体から取り外す必要もなくしました。
その結果、材料投入から圧縮、取り出しまでの一連の流れが途切れることなくスムーズに行えるようになり、作業効率は大きく向上しました。
この記事では、ストッパーを塩ビ管先端に一体化し、さらに分岐継ぎ手を使ってタネを横から投入できるように改良した具体的な加工方法と、その作業効率への効果について解説します。
ストッパー+投入口一体型成形管の作り方
コーキングガンのサイズを330mlから900mlに変更
今回の加工にあたっては、コーキングガンを従来の330mlタイプから、900mlタイプに変更しました。これまでは tajima の「コンボイジャスト(330ml)」を使用していましたが、圧縮できる容量が限られていたため、成形のたびにタネを詰め直す必要があり、作業効率が上がらないという課題がありました。
そこで今回は、より多くのタネを一度に圧縮でき、繰り返しの圧縮作業を減らせる900mlサイズを選択しました。選定したコーキングガンは同社の同じコンポイジャストシリーズであるため、使用感や取り回しに大きな違和感はなく、作業効率の向上に貢献することに期待します。
コーキングガンの変更に伴う塩ビ管サイズの再選定
コーキングガンのサイズを変更するにあたり、使用する塩ビ管のサイズも適切に選定する必要があります。従来使用していた330mlタイプのコーキングガンでは、対応できるカートリッジ径が⌀50mmまでに限られていたため、外径が約48mmのVU40が最も適合性の高い塩ビ管でした。
一方、今回使用する900mlタイプのコーキングガンは、適合カートリッジ径が⌀66mmまで拡大されているため、外径約60mmのVU50も対応範囲内となります。そのため、従来より太い塩ビ管を使用できるようになり、成形物の直径を広げたり、容量を増やしたりする自由度が高まりました。
分岐継ぎ手の導入によるタネ投入の効率化
塩ビ管をコーキングガンのホルダーから毎回取り外すことなく、タネを容易に投入できる構造とするため、分岐型の継ぎ手を塩ビ管に接続する方式を採用しました。
使用したのは、モノタロウブランドの中で選定した呼び径50のVU管に対応する分岐継ぎ手であり、選択肢としては「VU90°チーズ」「チーズ 大曲り VU90°」「VU45°Y」などがありました。
その中で今回は、装入できるタネの量をできるだけ多く確保したいという観点から、分岐部が比較的短く、コンパクトに構成されているT字型の「DV90°チーズ」を選定しました。
ちなみに、「チーズ 大曲り VU90°」や「VU45°Y」といった継手は、内部の曲がりが緩やかで、流体抵抗が少ない構造になっています。そのため、粘性の高いペースト状のタネを扱う場合は、流れを妨げにくい緩やかな分岐構造をもつ継手のほうが向いているかもしれません。
この継ぎ手をVU管に接続するにあたり、コーキングガンのホルダーから出し入れがスムーズに行えるようにするため、VU管は220mmの長さに切断しました。
なお、継ぎ手は接着剤を使用しなくても、奥まで差し込めばしっかりと固定されました。また、上下に傾けながら引っ張ることで再び取り外すことが可能なため、VU管の長さを微調整したり、加工することも可能です。
ストッパー一体化加工
従来は圧縮した成形物をコーキングガンで押し出す際、塩ビ管をクランプで固定する手間を省くために、先端にストッパーを噛ませて塩ビ管を固定し、クランプの着脱作業を省略していました。
しかし、ストッパーが別部品として存在していたため、毎回「取り付けや取り外し」の手間が発生し、作業のたびに位置合わせや装着に時間がかかるという課題が残っていました。
そこで、毎回のストッパー着脱を不要とし、作業の流れを途切れさせないようにするため、塩ビ管の先端にストッパー機能を一体化する加工を施しました。
今回の加工では、塩ビ管の先端にストッパー機能を一体化させるため、長さ約57mmの範囲で縦方向に半割する加工を施しました。
まず、正確な切断位置を把握するために、塩ビ管の先端に墨付け(印付け)を行い、切断範囲を明確にしました。
次に、切断には直進性を重視するためにPカッターを使用し、L型アングル材やリング状にした端材を定規として添えることで、塩ビ管の湾曲した表面でも安定したガイドが得られるようにしました。定規は何度かけがいて溝を掘れば、外しても問題ありませんでした。
Pカッターで複数回にわたって徐々に切り込みを深くし、貫通寸前まで丁寧にけがいたのち、最後は通常のカッターを使って貫通切断します。やや手間と時間はかかりましたが、仕上がりにムラのない、まっすぐで精度の高い半割加工が行えました。
なお、加工精度をそれほど要求しない場合や、作業時間の短縮を優先する場合には、刃にアサリのない鋸を使用して一気に切断したり、電動工具であれば「ミニルーター」や「グラインダー」を使い切断したほうが効率的です。
排水用の穴を加工する
タネの成形時には、含まれる水分を圧縮工程で適切に排出しなければ、十分な強度をもった成形体に仕上げることができません。水分が適切に抜けないと圧縮が不十分になり、密度の低い脆弱な仕上がりとなってしまいます。そのため、排水経路をあらかじめ確保しておく必要があります。
従来は直径4mmの穴をあけていましたが、穴が大きすぎるとタネの一部が圧縮中に穴から飛び出したり、穴に食い込んでしまったりすることがありました。このような状態では、成形後に取り出す際に余計な抵抗が生じ、コーキングガンのレバーを強く握らなければならない場面もありました。
そこで今回は、穴径を3mmに縮小し、タネの穴漏れや、食い込みによる負荷を軽減するように改良しました。穴は10mm間隔(ピッチ)で均等に配置し、8列にわたってあけることで、全体として十分な排水性能を確保しました。
スペーサーを作る
圧縮成形においては、塩ビ管先端に設けた半割ストッパー部の開口部からタネが飛び出さないように、開口部を一時的に塞ぐ「スペーサー」を設置する必要があります。タネはこの開口部より上方の空間で圧縮され、成形が完了した後、スペーサーを取り外して押し出すことで、タネを開口部からスムーズに取り出すことが可能になります。
なお、開口部の長さを約57mmとしたのは、厚さ19mmの1×4材から直径を揃えた円柱状のスペーサーを3枚作成し、これらを重ねて設置することで、ちょうど開口部全体を塞げるようにするためです。この円柱状パーツは穴の直径を自由に変えて穴あけ加工ができる自在錐で作りました。
コーキングガンの先端にあるホルダーの行き止まり部分は、カートリッジが抜け落ちないようにするためのストッパー構造になっていますが、これは円筒の外周だけに立ち上がりの壁がある構造で、中心部は大きく開口した状態になっています。この構造のため、ストッパー部のすぐ上に置いたスペーサーが中央の隙間から下へ抜け落ちやすくなっています。
スペーサーがコーキングガン先端の中央開口部から抜け落ちるリスクに対処するため、ストッパー部のすぐ上に丸く切り抜いた板を設置し、スペーサーの落下を物理的に防ぐ構造を検討しました。
ただし、作業中の振動や力の加わる環境下では、この板が外れてしまったり、割れたりする恐れがあるため、脱落や破損を防ぐために、耐衝撃性が強く弾性があるVUキャップ(呼び径50)の側面を半分に切り取り、残った部分を塩ビ管の半割部分に沿わせて接着するという方法に変更しました。
スペーサー取り出し時の問題点の発覚
期待を膨らませつつ、新たに改良したこの構造でタネの圧縮成形を試みたところ、いくつかの改善点と有効性が確認されました。まず、スペーサーの挿入には若干の手間がかかったものの、全体的な作業工程はこれまでよりも効率化されました。
また、分岐継ぎ手を採用したことで、塩ビ管を毎回コーキングガンから取り外す必要がなくなり、タネの投入作業が容易になった点は大きな進歩です。この変更により、これまで当たり前のように行っていた一手間が削減され、作業の流れがよりスムーズになりました。
その他に、排水穴の直径を従来より小さく加工したことで、圧縮時にタネが穴から飛び出すことがなくなり、周囲が汚れるといった問題が解消されました。
ただし、排水穴の数が多いほど圧縮時の抵抗が減り、作業が楽になる傾向が見られるため、穴をあける列をもう少し増やしておくべきであったと感じました。
穴の直径を小さくしたことにより、タネが穴に引っかかることがなくなり、比較的軽い力でもスムーズに押し出すことが可能になりました。
その他に、成形物の側面に生じる凹凸が小さくなりました。その結果、外観がより滑らかで整った仕上がりになりました。
改善点は、スペーサーの脱落を防ぐ目的でVUキャップを塩ビ管に接着していたことにより、スペーサーを横方向にスライドさせて取り出すためのクリアランス(逃げや遊び)が失われ、取り外せなくなってしまいました。
逃げや遊びを確保するため、塩ビ管に接着していたVUキャップは、使用時には取り外す方式に変更しました。接着部分はホットガンで加熱して玄能で打撃を加えれば、簡単に取り剥がすことができました。
もともと塩ビ管は、ホルダーにスムーズにセット・取り出しができるよう、わずかに短めに切断してありました。このため、VUキャップと塩ビ管を離すことで端に僅かな隙間(遊び)が生まれ、スペーサーを横方向にスライドさせるためのクリアランスが確保され、取り出しがスムーズに行えるようになりました。
その他に、この遊びがあることで、スペーサーの設置作業も格段に簡単になり、無理な力をかけずに所定の位置に収めやすくなりました。また、成形後のタネもストレスなく開口部から取り出せるようになり、作業全体の効率と安定性が向上しました。
追記:改良
当初、3枚の板で構成されたスペーサーを1枚ずつはめ込み+取り外しを行っていました。作業効率をよくしたつもりが、地味に手間がかかっていました。そこで、3枚の板をビスで接合し、1つのパーツとしてワンアクションで扱える部品にしました。さらに、取手を取り付けることで、設置と取り出しをしやすいようにしました。さらには、塩ビ管に指で押し出せる穴を設け、成形物の取り出しやすさも改善しました。
圧縮成形後の強度と扱いやすさ
使用する塩ビ管のサイズを拡大したことで、成形される薪の直径は従来の約42mmから約53mmへと大きくなりました。しかし、使用したのが900mlタイプのコーキングガンであっても、330mlタイプと同様に圧縮成形は問題なく行えました。
圧縮後の成形物はしっかりと固められており、適度な強度と接合力を備えているため、乾燥させる際に手荒に扱っても容易に崩れることはありません。また、シュレッダーで裁断し、熱湯で柔らかくした短冊状の状態で圧縮しても、しっかり成形することが可能でした。
短尺の成形薪は長尺の成形薪に比べると、燃焼時間が短くなる短所があります。しかし、小型のウッドガスストーブでは短い薪の方が着火しやすく、火力も強くなる傾向があるため、短時間で強火が必要な湯沸かしから、インスタントのラーメンやチャーハンなどの調理に向いています。
製作過程を動画で紹介
この記事では、ストッパーを塩ビ管先端に一体化し、さらに分岐継ぎ手を用いて横から原料を投入できるよう改良した圧縮成形薪の構造について解説しました。実際の作業手順や使用の様子をより詳しくご覧になりたい方は、YouTubeの動画をご視聴ください。
コメント